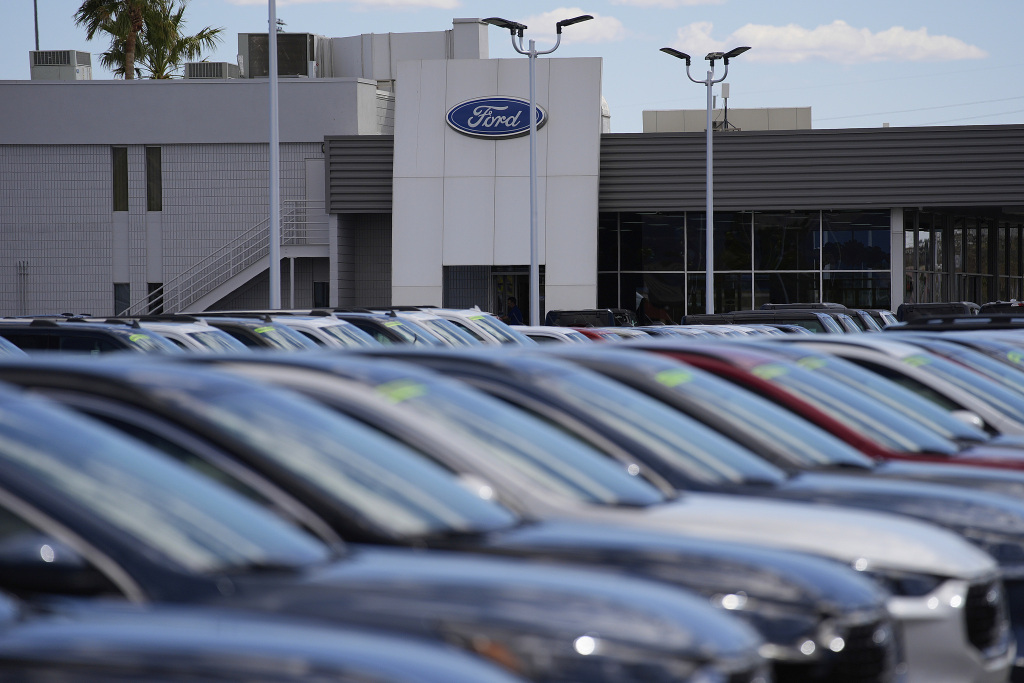
A brand new white 2025 Ford Expedition SUV, with bronze exterior trim, rolls off the production line at Ford's Kentucky Truck Plant, where American workers meticulously build the vehicle from frame to finish.
However, it is far from being "Made in the USA" as people imagine. More than half of the major parts of this car, at least 58%, are "imported", of which 22% are from Mexico. Even the "heart" of the vehicle, the 3.5-liter twin-turbocharged V-6 EcoBoost engine, although designed by Ford, is not a native American product.
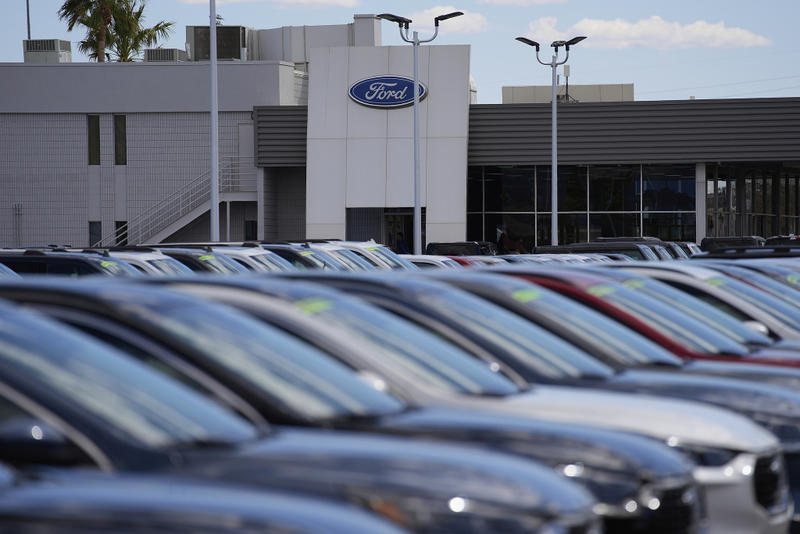
On April 4, 2025, local time, in Las Vegas, Nevada, a Ford car dealer displayed a number of SUVs.
This popular large SUV vividly demonstrates the complexity of the global automotive supply chain and ruthlessly reveals a reality: even a veteran American automaker like Ford relies heavily on foreign parts for the cars on its domestic production lines in the United States.
The massive Kentucky assembly plant, which employs more than 9,000 people and builds the Expedition and F-Series pickups and Lincoln Navigator SUVs, is exactly the kind of plant the Trump administration has been pushing automakers to build in the United States through its aggressive tariffs.
After Trump imposed a 25% tariff on imported cars and parts, automakers responded by vigorously promoting investment in the United States and making every effort to localize their supply chains. Although full local production can bring jobs and economic growth to the United States, experts agree that this is simply not feasible in reality.
Martin French, a senior supplier executive and partner at Berylls Strategic Consulting, said bluntly: "For some parts that have been outsourced abroad, even with tariffs, the cost of mass production locally is still lower than in the United States."
There are not enough processing plants for steel, aluminum, semiconductor chips and other products, especially old chip plants for automobiles, as well as raw material production sites such as platinum and palladium, in the United States. If all domestic production is to be met, a large number of new factories and mines need to be built. Experts estimate that it will take at least ten years to achieve this goal.
In addition, the soaring cost of manufacturing cars across the United States will make many consumers reluctant to buy them, which will lead to a decline in demand and a possible reduction in production scale.
“We could move all of our production back to the U.S., but if every Ford car sold for $50,000, we wouldn’t be able to survive,” Ford CEO Jim Farley said on “Squawk Box.” “That’s the balancing act that every automaker has to deal with, even the most American of them.”
Farley also pointed out that 15% to 20% of the current commoditized auto parts are extremely difficult or even impossible to source in the U.S. These parts include small fasteners, labor-intensive wiring harnesses, and semiconductor chips worth nearly $5,000 per vehicle, most of which come from Asia.
According to the S&P Global Mobility Report, an average car has 20,000 parts after being disassembled, and these parts may come from 50 to 120 different countries. For example, the Ford F-150, although only assembled in the United States and sharing the platform and some parts with the Expedition, has about 2,700 major billable parts, not including many small parts.
The Trump administration has tried to ease the high cost of making cars in the U.S. through tax breaks or consumer incentives, like the previous $7,500 tax credit for electric vehicles. But it turns out that a 100% American-made car is far more expensive and complex than imagined. And because automakers are required to report the combined proportion of American and Canadian parts, rather than the proportion of American parts alone, it makes it more difficult to track domestic parts.
Several auto analysts and executives revealed that material costs alone (excluding manufacturing investment) will add thousands of dollars to the price of a car, which will not only squeeze automakers' profits but will also be passed on to consumers, leading to higher car prices.
Mark Wakefield, partner and global automotive market head at AlixPartners, said that although time can solve all problems, as automakers move closer to 100% "Made in the USA", investment and additional costs in procuring parts from the United States and Canada will increase exponentially.
“The closer you get to 100 percent, the more expensive it is. Getting to above 90 percent is expensive, and getting to around 95 percent is prohibitively expensive, and a lot of things take a lot of time,” he said.
Wakefield pointed out that achieving the last 5% to 10%, if possible at all, would be costly and could take more than a decade to establish a raw material procurement system and relocate production of some components.
He believes: "At present, no matter how much it costs, it is difficult to exceed 95% on average. Because a large number of facilities need to be built, and the construction of facilities related to processing and raw materials is not only time-consuming, but also requires billions of dollars of investment."
Executives from two auto parts suppliers told the media that under the current circumstances, it is almost impossible for automakers to profitably produce 100% American-made cars. Another automaker executive estimated that the cost of a full-size pickup truck assembled in the United States would increase by at least $7,000 if it were to source as many parts as possible from the United States and Canada.
Experts estimate that increasing the proportion of U.S./Canadian parts in a car below 70% to 75% or 80% could increase costs by $5,000; increasing it to 90% would require an additional $5,000 to $10,000; and costs would continue to rise if a higher proportion is to be achieved.
According to Cox Automotive, the average transaction price of a new car in the U.S. is currently about $48,000. Assuming that the cost of materials and parts for a car is $30,000, plus the above cost increase, automakers will need to spend about $10,000 to $20,000 more.
Overseas automotive media Cars.com reported that the United States is the country with the highest automobile manufacturing costs in the world. Data shows that the average price of a new car assembled in the United States is more than $53,200, while Mexico is about $40,700, Canada is $46,148, and China is about $51,000.
In theory, without considering raw materials, someone could start a new company called "American Motors" from scratch, invest billions in new factories, and create a supply chain across the U.S. But experts point out that the cars produced in this way would not only be low in volume, but also ridiculously high in price.
Take Ferrari as an example. Every car of this Italian car brand is produced in Italy, and domestic parts are used as much as possible. However, even so, many parts or raw materials such as airbags, brakes, tires, batteries, etc. of Ferrari sports cars still come from suppliers outside Italy.
“If you produce it at very low volumes and you’re very innovative in the vehicle, you could probably produce a $300,000 to $400,000 all-American car,” Wakefield said. “But to do it at scale, it’s probably going to take 10 to 15 years and $100 billion.”
What is a more realistic goal? Wakefield believes that increasing the proportion of American and Canadian parts in cars to 75% and completing final assembly in the United States is a more feasible goal that "will not force automakers to make uneconomical decisions," and some models have already reached this standard.
But to achieve this goal on a large scale, automakers and suppliers still need to invest billions of dollars to localize production. Some automakers will make the transition relatively easy, while others will need to make major adjustments in parts procurement and production.
According to the latest data from the National Highway Traffic Safety Administration, among the 2025 models, the Kia EV6, two Tesla Model 3s, and the Honda Ridgeline AWD Trail Sport have a U.S./Canadian component share of 75%. Nearly 20 other models have a share of 70% or more, and data for some models are still being collected.
Compared with the data in 2007, the gap is obvious. At that time, the top 16 models (all from GM and Ford) had more than 90% of American and Canadian parts, and the Ford Expedition was as high as 95%. But that was before the globalization of the automotive industry's supply chain accelerated after the Great Recession, and before the significant advancement of automotive technology and the increasing importance of new parts and materials.
Research from American University's Kogod School of Business shows that the U.S./Canadian content of vehicles has been declining for decades, driven by the globalization of supply chains and increased sourcing of parts from Mexico.
Data from Cars.com shows that among the 2019-202 models, the top 10 models with the highest U.S. and Canadian parts content have an average share of between 63.6% and 69.2%.
Many imported luxury brands, such as German automakers and Toyota's Lexus, purchase very few parts in the United States, with some models even purchasing zero or only 1%.
According to the 1992 U.S. Automobile Labeling Act, the percentage of U.S./Canadian parts is calculated by "model series", rounded to the nearest 5%, calculated by automakers and reported to the government. However, it should be noted that a high percentage of North American parts does not mean that the vehicle is produced in the United States. For example, the 2024 Toyota RAV4 has a U.S./Canadian content ratio of 70%, but it is produced in Canada.
"In theory, a car made in the U.S. could have as little as 1% U.S. content," said Patrick Masterson, lead researcher on Cars.com's Made in America Index. Masterson said attention to the index has increased significantly this year amid Trump's tariffs and nationalist sentiment.
He said: "The number of visits to the American Manufacturing Index has skyrocketed this year... People's attention to this issue has never been higher." He also emphasized that "it is extremely difficult to make a car that is 100% made in the United States."